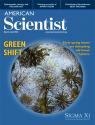
This Article From Issue
March-April 2016
Volume 104, Number 2
Page 67
DOI: 10.1511/2016.119.67
To the Editors:
The article “Bessemer’s Volcano and the Birth of Steel” by Ainissa Ramirez (Technologue, January–February) relies a bit too much on inventor Henry Bessemer’s autobiography and fails to give proper credit to others involved in the early mass production of steel. In particular, the inventor William Kelly of Kentucky actually invented the pneumatic process several years before Bessemer. Kelly recognized that the exothermic reaction of oxygen in the air with carbon and other impurities in molten iron ore would sustain the melt when air was forced through it, thus purifying the iron and reducing fuel costs.
Whether Bessemer knew of Kelly’s prior work is unlikely ever to be known, but his mid-1850s patents prompted Kelly to appeal to the U.S. patent office. The evidence he provided was deemed convincing, so Kelly received the U.S. patent with priority. Kelly sold his patent to owners of the Kelly Pneumatic Process Company of Wyandotte, MI, which later merged with Bessemer patent owners in order to make steel in the United States. The engineer Robert Mushet, not Bessemer, was first to make the critical deduction that removing all the carbon from molten impure iron, then adding back a measured amount was the most reliable way to make steel. Bessemer’s wealth, tilting converter invention, and skill as an entrepreneur contributed greatly to the ubiquitous use of steel in railroads, buildings, and so on, but he did not invent the so-called “Bessemer Process.”
The American Chemical Society recognized Kelly’s work with a National Historic Chemical Landmark in Eddyville, KY, in 2015.
William R. Oliver
Crittenden, KY
Dr. Ramirez responds:
Thank you to Dr. Oliver for commenting on the role of William Kelly in steel’s early mass production, bringing up an interesting and widespread misconception about the inventor. I interviewed historian Robert Gordon of Yale University, who has done extensive research on Kelly. Gordon stated that Kelly’s role in steel’s early mass production is largely a myth: “There is no evidence to support the idea that Kelly made steel with a converter. Secondly, the artifact that was displayed in the Smithsonian and labeled as a Kelly Converter was actually a Bessemer converter. There is some evidence that this converter was made in England.”
William Kelly was in the business of transforming pig iron into wrought iron by a finery process. One of the steps in this well-known process is to use a blast of air to reduce the silicon content to create wrought iron. Kelly had some good ideas to run his operation more effectively. His unique contribution was to run the hot metal into the refinery forge, where the air blast is used to reduce the silicon content. That makes it easier to make the final product of wrought iron, not steel.
The Kelly myth, which continually gets revived, has many layers of business, money, and politics that read like a novel. I will include some of these details in my forthcoming book.
To the Editors:
In the January–February issue, Ainissa Ramirez makes a number of errors in her Technologue column in the paragraph describing “the secret behind steel” on page 13.
Modern steels today come in many varieties, both multiphase mixtures or single-phase alloys. They range from plain carbon steels to multicomponent alloy steels. Only one specific composition (the eutectoid) has a completely lamellar, or finely layered, structure. The two phases that make up this structure are cementite (an intermetallic compound, Fe3C) and ferrite (a random solid solution of carbon in iron). Ferrite is not a compound.
Michael Notis
Lehigh University, Professor Emeritus
Bethlehem, PA
Dr. Ramirez responds:
The term steel applies to a range of iron-carbon alloys, so I understand Dr. Notis’s point of view. But it would not be fair to say that my piece was full of errors.
There are many terms that would more precisely explain the microstructure of steel—such as phase, eutectoid, solid solution, lamellar structure, and others—but general readers (even those with scientific backgrounds) may not be familiar with them. As such, I employed general science nomenclature, like the word compound, to differentiate ferrite from the other constituents of steel. For a metallurgist (myself included), compound might not fully describe things perfectly, but the spirit of the phrase is to explain how this one part differs from another. I believe I make this point clearly in the text.
This criticism illuminates the debate in science communication over precision versus access to information. The more precise the scientific vernacular, the less general audiences will comprehend the meaning of what is expressed. In writing this piece, I was thoughtful about my explanations of steel, drawing from my experience teaching materials science at Yale University. My aim is to broaden access to and interest in materials science. As such, I chose to use terms that get a concept across more readily than highly technical terms. Precision may be lost, but, for me, increasing the number of people who master the concepts outweighs it.
I kindly thank Dr. Notis for his informed remarks. I appreciate the opportunity to display the difficulty of and the choices made in bringing understandable science to the general public.
American Scientist Comments and Discussion
To discuss our articles or comment on them, please share them and tag American Scientist on social media platforms. Here are links to our profiles on Twitter, Facebook, and LinkedIn.
If we re-share your post, we will moderate comments/discussion following our comments policy.